Innovation in wildlife conservation demands not only passion but also cutting-edge technology. Dr. Constance Woodman, a research scientist at Texas A&M University College of Veterinary Medicine, has partnered with Sean Ragan, owner of a rapid prototyping and bespoke manufacturing facility in Austin, Texas, to develop custom tools using Raise3D’s advanced 3D printing technology. Together, they are revolutionizing the way researchers monitor bird behavior around the world, producing innovative devices that collect critical data with minimal environmental disruption.
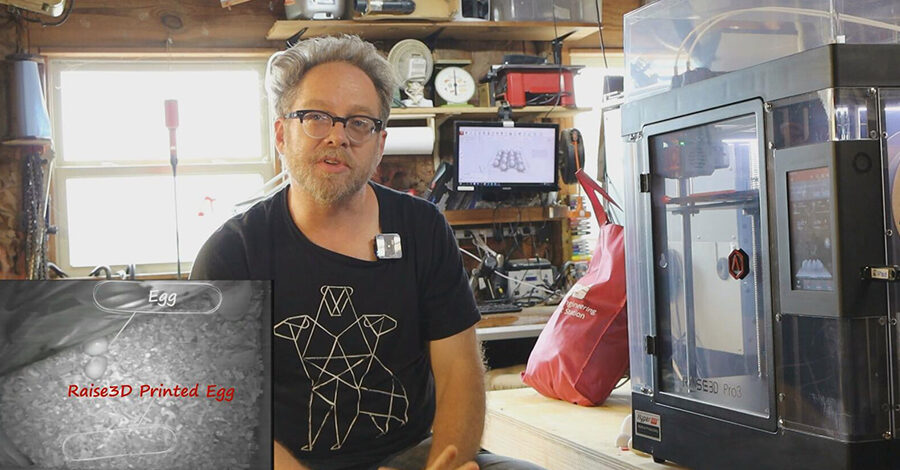
Dr. Constance Woodman partnered with Sean Ragan developing custom tools
Unique Requirements of Specific Species
Conservation research requires specialized, adaptable equipment to monitor animals in the wild, particularly birds, where data gathering needs to be as non-invasive as possible. Traditional tools were either too generic or unable to meet the unique requirements of specific species. The equipment had to be highly customizable, capable of integrating specialized scientific instruments, and durable enough to survive diverse environmental conditions across multiple regions.
Scientists studying bird behavior needed a solution that allowed rapid design iterations, small-batch production, and custom designs for varying payloads and species. They required tools that could be tailored quickly to meet evolving scientific demands without compromising on quality or durability.
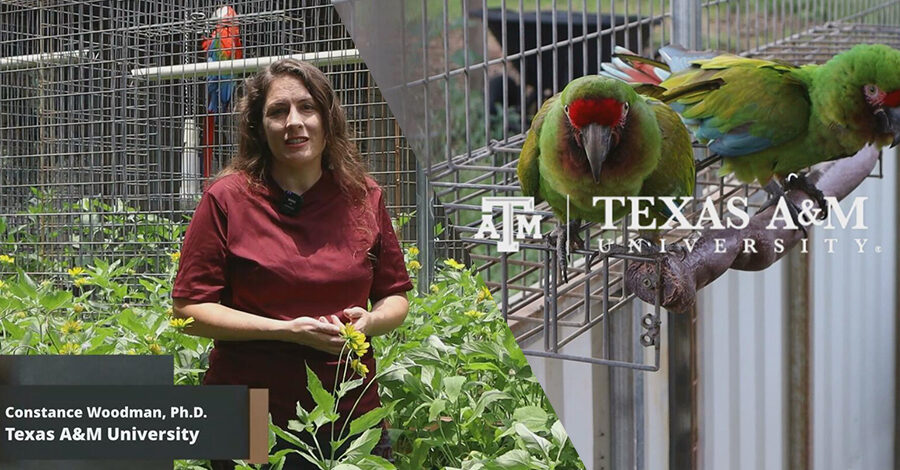
Conservation research requires to monitor animals in the wild
Creating Intricate Designs with Raise3D Technology
Dr. Woodman and Sean Ragan turned to Raise3D’s Pro3 Plus and E2 3D printers, which provided the versatility, precision, and speed needed for custom conservation tools.
The Raise3D Pro3 Plus is renowned for its dual extruder system, enabling the production of complex parts that require different materials, and is perfect for creating intricate designs like the smart eggs used to monitor bird nesting behavior. With a print volume of 300 x 300 x 605 mm, the Pro3 Plus offered ample space to create larger prototypes, while its automatic bed leveling and air flow manager ensured reliable, high-quality prints. The printer’s interchangeable hot ends allow for greater flexibility, easily switching between filament types, depending on the material requirements of each research project.
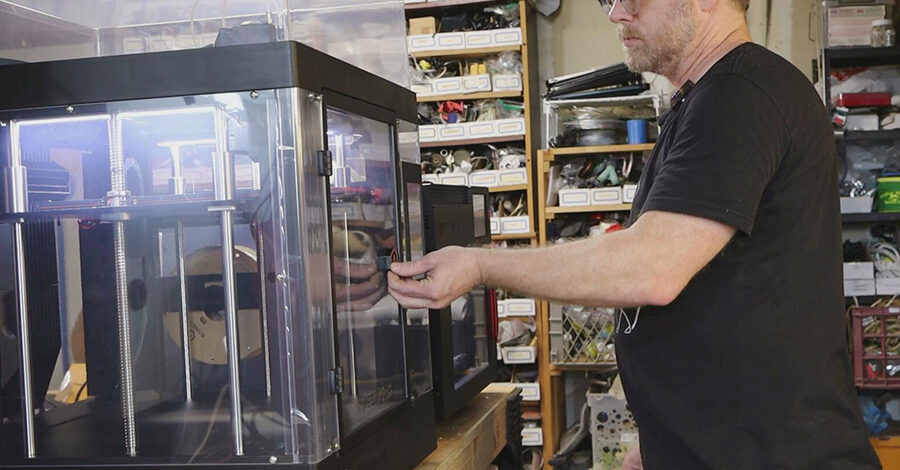
Raise3D Pro3 Plus is perfect for creating intricate designs
For applications where even more complex design was needed, the team relied on the Raise3D E2. This desktop 3D printer can print with a variety of different filaments, and its unique extruder gear design enables it to use flexible 3D printing materials, more reliably and with better results. The E2’s Independent Dual Extruder (IDEX) technology also enabled the creation of more complex designs, reducing print times and improving overall efficiency.
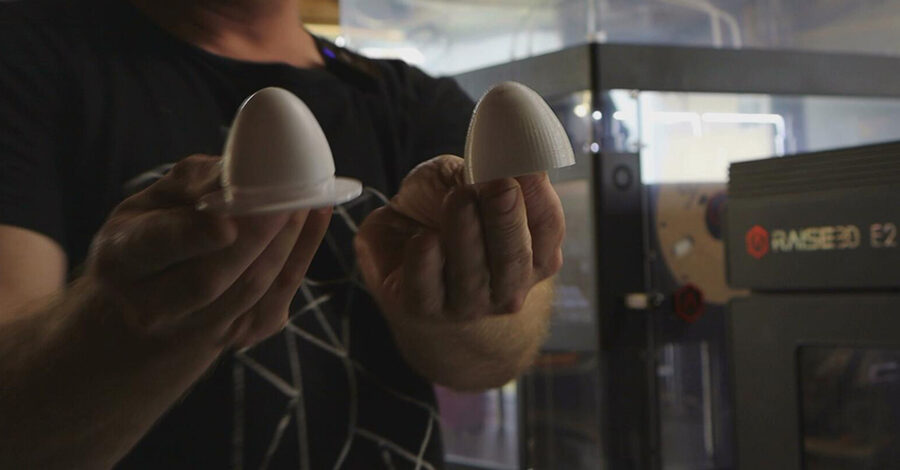
IDEX technology also enabled the creation of more complex designs
Additionally, Raise3D’s Open Filament Program (OFP) provided flexibility for the conservation team. The ability to use a variety of third-party filaments meant Dr. Woodman and Ragan could experiment with different materials to best suit the varying needs of the projects, from creating watertight threads on the smart eggs to developing lightweight enclosures that could house intricate scientific equipment. This flexibility was key in developing products that were adaptable to specific environments, ranging from wetlands to arid islands.
The standout feature for the team was Raise3D’s Hyper Speed technology, a game-changer for researchers working on tight timelines. Hyper Speed allowed for much faster print speeds without sacrificing precision, ensuring that custom prototypes could be printed quickly and accurately. This rapid prototyping capability was crucial for meeting the needs of scientists working around the world, allowing them to modify designs and deploy equipment faster than ever before.
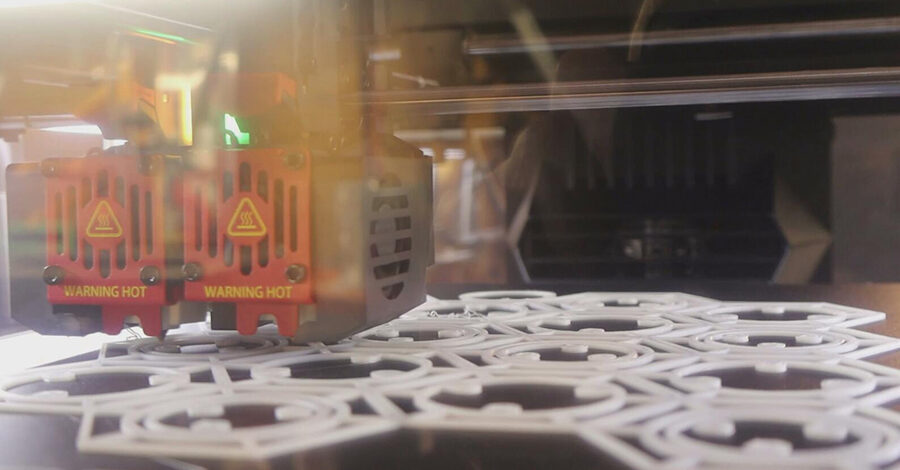
Raise3D’s Hyper Speed technology is a game-changer
Greater Flexibility and Customization
The integration of Raise3D’s Pro3 Plus, E2, and Hyper Speed technology into their rapid prototyping workflow enabled Dr. Woodman and Sean Ragan to significantly enhance the precision, durability, and efficiency of their custom conservation equipment.
The smart eggs and smart nests created with Raise3D’s technology are now used by scientists globally, from New Zealand to the South Sandwich Islands, helping monitor bird behavior and nesting patterns with minimal disruption to the wildlife. The custom-designed enclosures house sensitive electronics that track and log critical data, which is then used to inform conservation strategies. Each design is tailored to the specific species being studied, allowing for greater flexibility and customization of the payloads, all of which are made possible by Raise3D’s 3D printing technology.
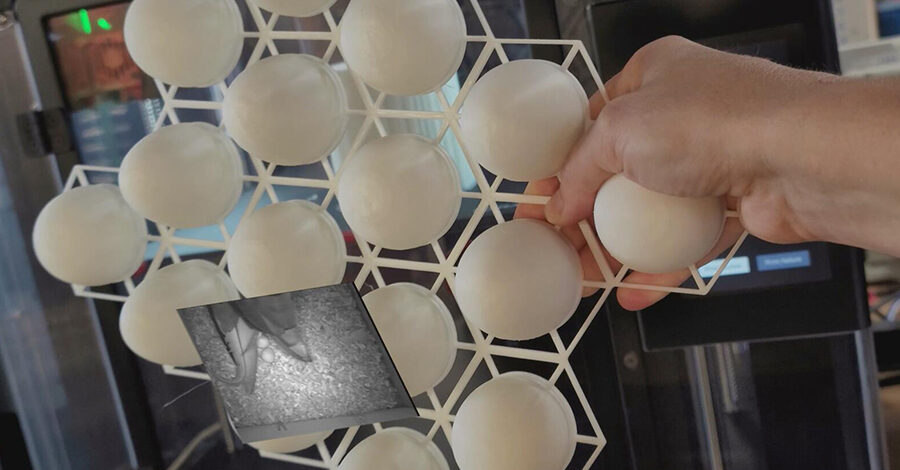
The smart eggs created with Raise3D’s technology
The Pro3 Plus and E2 printers have enabled the team to rapidly prototype and manufacture parts in small batches, making it possible to create highly specific, short-run products. Raise3D’s Hyper Speed technology drastically reduced print times, enabling quick turnaround on modifications and new designs, which was vital for responsive and adaptive research.
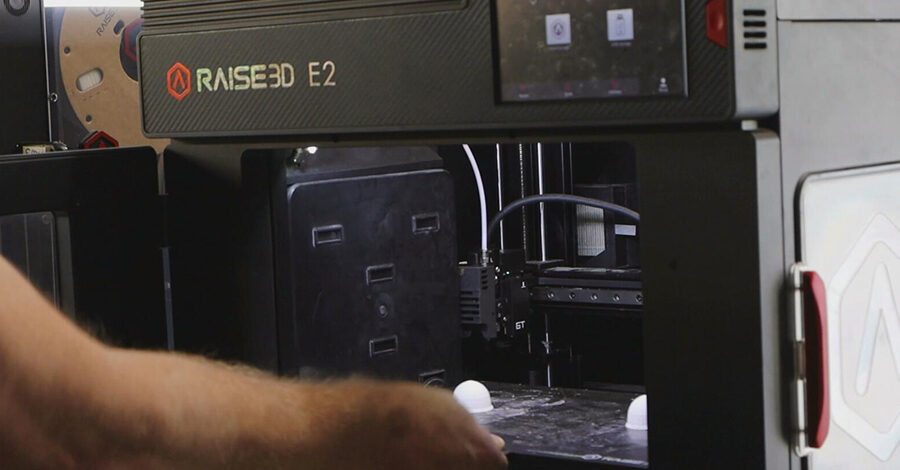
Create highly specific and short-run products
Leading the Charge in Conservation Innovation
Through their partnership with Raise3D, Dr. Constance Woodman and Sean Ragan are leading the charge in conservation innovation, using advanced 3D printing technology to create custom solutions for wildlife research. With Raise3D’s Pro3 Plus, E2, and Hyper Speed technology, they are able to produce high-quality, bespoke conservation tools that are used by scientists across the globe. This collaboration highlights the power of rapid prototyping and bespoke manufacturing in revolutionizing how we protect and study the natural world.
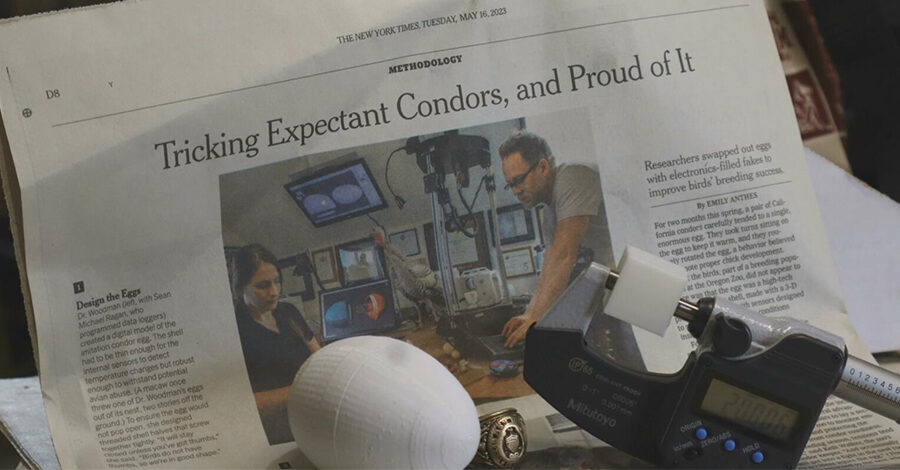
The power of rapid prototyping and bespoke manufacturing